Vase räbu on räbu, mis tekib pärast vasemaagi sulatamist ja ekstraheerimist, tuntud ka kui sularäbu.Räbu töödeldakse purustamise ja sõelumise teel vastavalt erinevatele kasutusviisidele ja vajadustele ning spetsifikatsioone väljendatakse silmaarvu või osakeste suuruse järgi.
Vase räbu on kõrge kõvadusega, teemandiga kujuga, madala kloriidioonide sisaldusega, liivapritsi ajal vähe tolmu, ei saasta keskkonda, parandab liivapritsiga töötavate töötajate töötingimusi, rooste eemaldamise efekt on parem kui muul rooste eemaldamise liival, kuna seda saab taaskasutadad, majanduslik kasu on samuti väga märkimisväärne, 10 aastat, remonditehas, laevatehas ja suured teraskonstruktsioonide projektid kasutavad rooste eemaldamiseks vasemaagi.
Kui on vaja kiiret ja tõhusat pihustusvärvimist, vase räbuon ideaalne valik.
Terasräbu töötlemisprotsess on eraldamise eesmärgilräbu erinevad elemendid.See hõlmab terase sulatusprotsessis tekkiva räbu eraldamise, purustamise, sõelumise, magneteraldamise ja õhust eraldamise protsessi.Räbus sisalduvad raud, räni, alumiinium, magneesium ja muud elemendid eraldatakse, töödeldakse ja taaskasutatakse, et oluliselt vähendada keskkonnareostust ja saavutada ressursside tõhus kasutamine.
Tooriku pinnaviimistlus pärast terasräbu töötlemist on üle Sa2,5 taseme ja pinna karedus on üle 40 μm, mis on piisav üldiste tööstuslike katmisvajaduste rahuldamiseks.Samal ajal on töödeldava detaili pinnaviimistlus ja karedus seotud terasräbu osakeste suurusega ja suurenevad osakeste suuruse suurenemisega.Terasräbu omab teatud muljumiskindlustd saab taaskasutada.
Efekti kontrast:
1. Proovide trea pinnaviimistluse jälgimineErinevate lihvimismaterjalidega on leitud, et vase räbuga töödeldud tooriku pind on heledam kui terasräbu oma.
2. Töödeldud tooriku karedusvase räbu on suurem kui terasräbu oma, peamiselt järgmistel põhjustel: vase räbu servad ja nurgad on teravamad ning lõikeefekt on tugevam kui terasräbu oma, mistõttu on lihtsam töödeldava detaili karedust parandada.
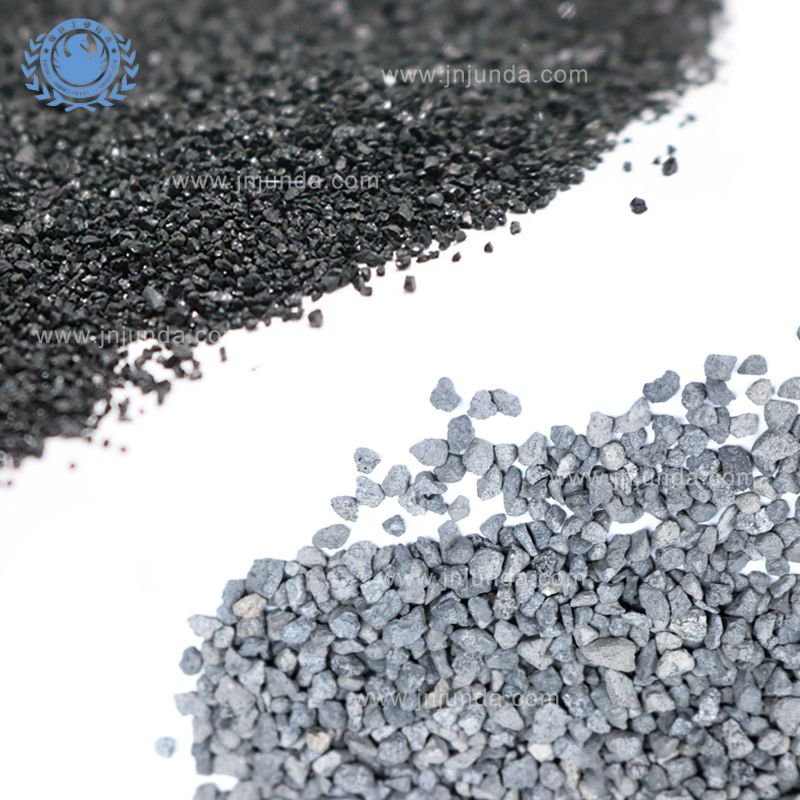
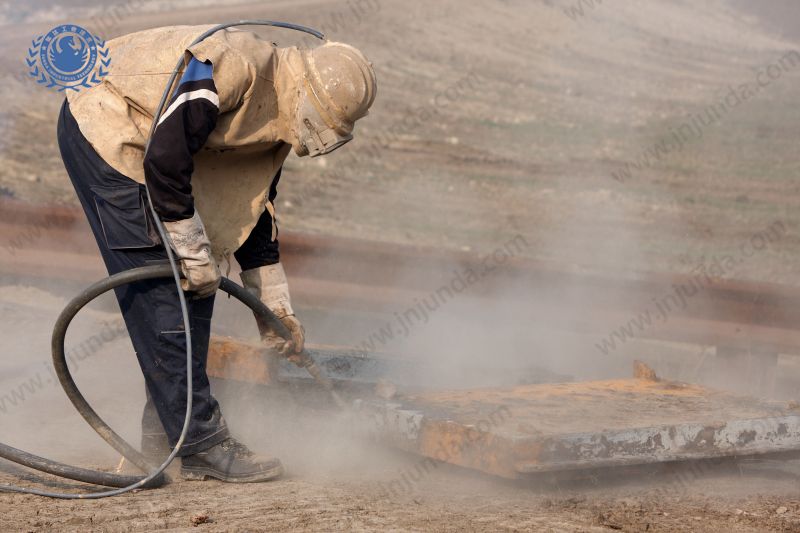
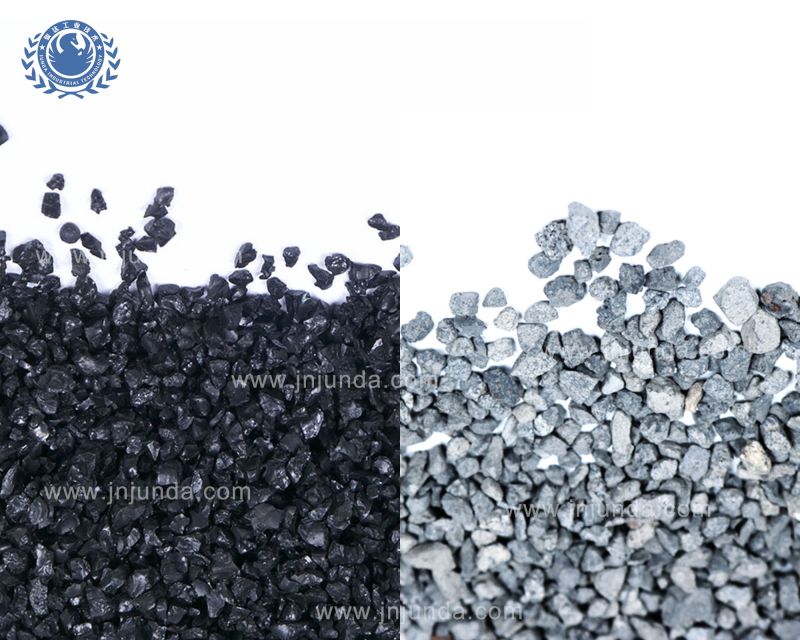
Postitusaeg: 21. märts 2024